Project OPTHERM – Optimization of FLM process by thermodiagnostics
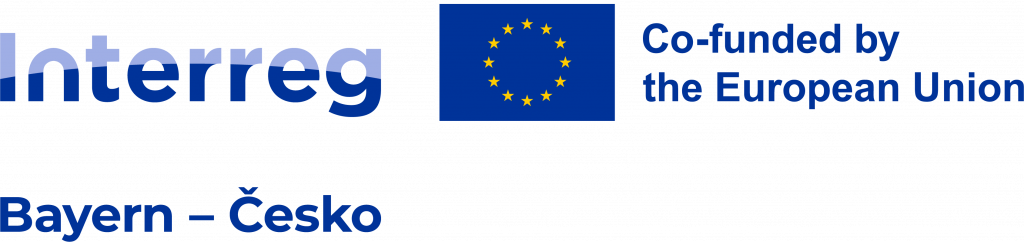
Project title
Optimization of FLM process by thermodiagnostics
(project acronym OPTHERM)
Identification code
BYCZ01-037
Funding provider
European Regional Development Fund (ERDF)
Ministry of Regional Development CZ
Programme
INTERREG Bavaria – Czech Republic 2021-2027
Project coordinator
University of West Bohemia in Pilsen / New Technologies – Research Centre
Project partner
Technical University of Applied Sciences Regensburg
Project start
06/2023
Project end
05/2026
Total project cost
848 852 EUR
Abstract
3D printing has widely established itself in industry, e.g., in prototype construction, and is also successfully used in small series production or in the construction of production equipment. The FLM (Fused Layer Modeling) process especially benefits from a low-cost, flexible, and easy-to-handle system technology, which is especially profitable for SMEs due to an enormous variety of printable materials. However, it is limited by the insufficient mechanical strength of the parts in the printing direction. The reason for this is the low layer adhesion resulting from a reduced temperature in the process zone. For this reason, mechanically stressed functional parts are rarely produced using FLM. This problem is addressed by the Infrared Technologies Laboratory of the UWB in Pilsen and the Laser Materials Processing Laboratory of the OTH Regensburg in the OPTHERM project. With the help of online temperature monitoring and an FEM simulation model, the project team wants to develop an approach to increase component strength. The involvement of companies (especially SMEs) already takes place during the definition of the requirements for the system to be developer and ends in a “Strong enough” campaign, which serves to optimize the component quality on site. Thus, SMEs are enabled to fully exploit the potential of FLM 3D printing and strengthen their competitiveness.
Project aim
The aim of the project is to optimize the conventional FLM 3D printing process using a thermodiagnostic approach. For this purpose, the process temperature is to be measured during printing by a self-developed miniature IR camera and the layer bonding is to be estimated based on this. With the help of the correlation between process parameters, temperature, and mechanical strength, it is possible to make precise statements about the process parameters that are required for optimal welding. This is supported by a process simulation to be developed in the project, which calculates the three-dimensional temperature field during printing. The measurement system and the correlations will also provide the basis for a temperature control system that will guarantee optimum layer welding at all times. This approach is to be qualified in an industrial demonstrator, which, in addition to an educational demonstrator, will be used for technology and innovation transfer within the program region.
Contact